Process hazard analysis (PHA)
Process hazard analysis
A process hazard analysis is a step-by-step review of chemical and manufacturing plant operating procedures. The goal of a process hazard analysis is to identify potential causes and evaluate the consequences of hazardous chemical releases. A process hazard analysis process helps organizations identify risks from equipment failures to human factors. The process hazard analysis helps to improve safety, prevent downtime and protect the environment. Process facilities in the United States are required by OSHA to run a process hazard analysis every five years. To conduct the process hazard analysis companies often use HAZOP.
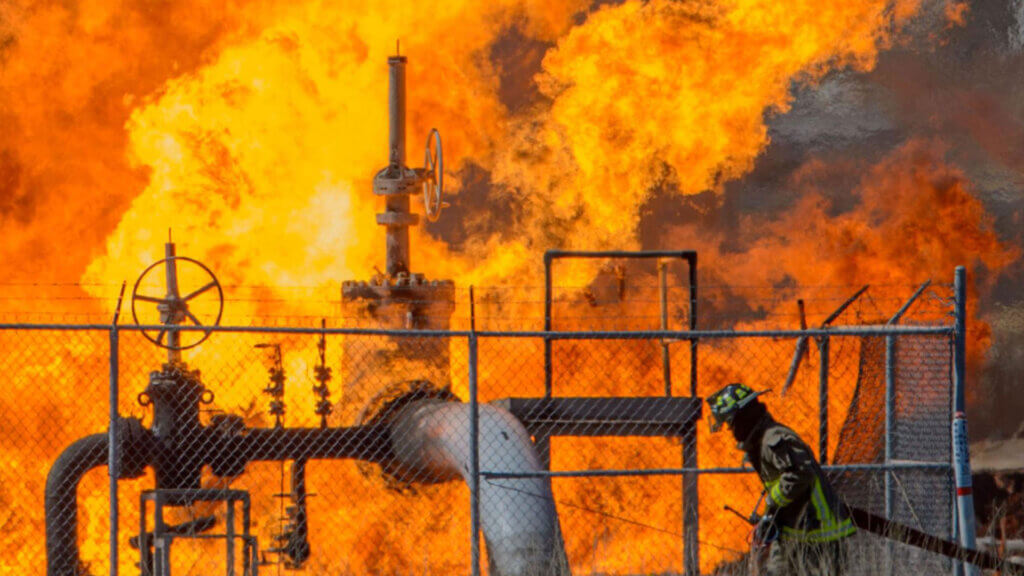
When should a process hazard analysis be conducted?
A process hazard analysis should be conducted for each stage of design, operation, and shut down. They are required to be completed initially and revalidated every five years. Major changes made to a process warrant a total re-do to be conducted earlier. Also, when either temporary or permanent modifications are made to a hazardous process, a Management of Change (MOC) process hazard analysis should be conducted to evaluate the inherent hazards that can result from the change.
What is the difference between a process hazard analysis and a LOPA?
A process hazard analysis covers a multitude of methods including HAZOP, what-if, and checklists. These are essentially to help companies to come up with scenarios that could potentially result in a process incident. Each of these scenarios are then analysed (usually qualitatively) to determine if the amount of safeguards that are available are appropriate for the level of risk. LOPA is a more detailed level of analysis of a known scenario. Where process hazard analysis is primarily utilised to identify hazards that are not currently known, LOPA is used to understand a known hazard scenario in a greater level of detail.
Why are companies adopting LOPA?
Process facilities in the United States are required by OSHA to run a process hazard analysis (PHA) every five years. The most common tool used to conduct the process hazard analysis is a qualitative method of analysis called HAZOP. Process safety professionals have reported a trend for PHA’s to go one step further than a HAZOP, in a quantitative study of risk termed and many scenarios are pushed to a Layer of Protection Analysis, or LOPA. A LOPA study quantitively analyses the risk of an event occurring. Commonly, companies reference quantitative values for risk set out in the Initiating Events and Independent Protection Layer in Layer of Protection Analysis manual created by the Center for Chemical Process Safety. Most organizations have adopted this book as the standard for defining and quantifying risks in initiating events and will use this book for defining layers of protection.
Simplify manual valve operations
LOPA’s often leave teams with difficult task of trying to solve complex problems, without creating complex and expensive solutions. One very common example of this is trying to simplify a manual process without the complexity of full automating the process.
Applications where teams need to control the sequence of an operating valves in a manual process include that are identified in a LOPA are:
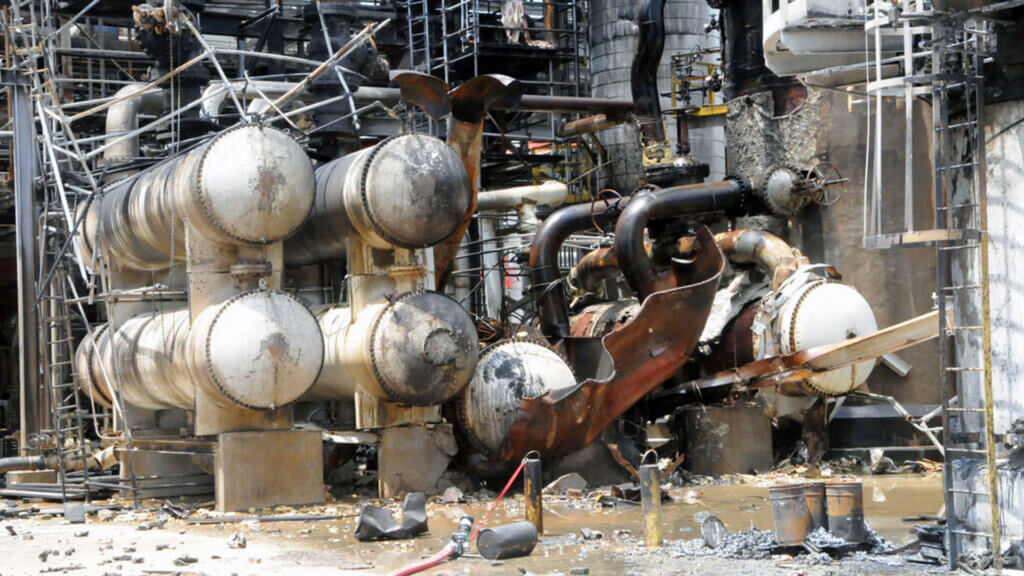
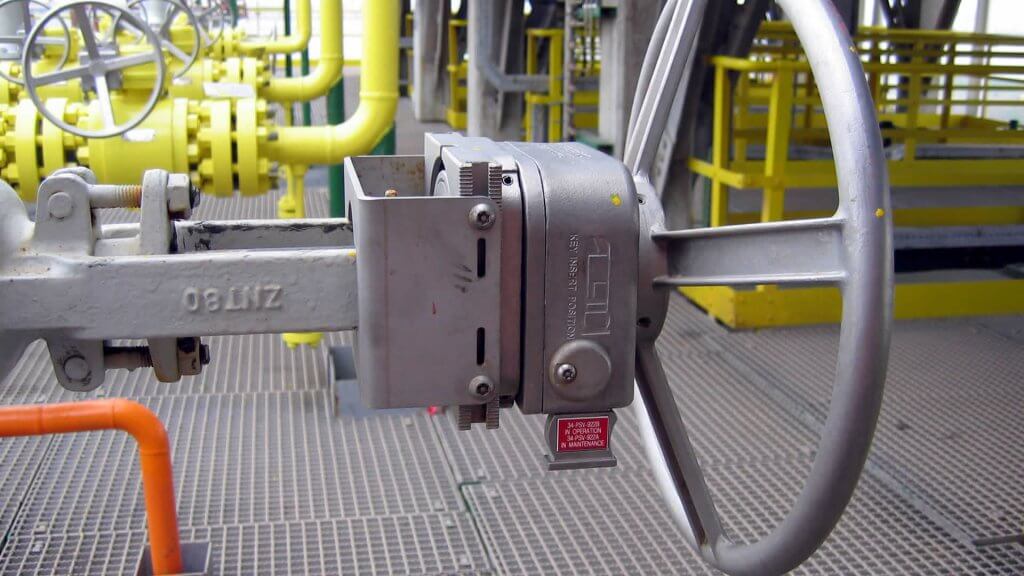
Using captive key systems to control manual valve operations
The most effective and simplistic solution for these complex scenarios lies on page 227 of the Initiating Events and Independent Protection Layers book, under the heading Captive Key. Captive key systems employ the use of locks that prevent the movement of valves and unique keys that will only be released in the desired valve sequence, preventing humans from operating valves in the incorrect sequence.
Achieve risk reduction by implementing captive key systems
The CCPS Guidelines subcommittee recommends that a Probability of Failure on Demand factor of .01 be awarded for Captive Key being used to controlling sequences. This means that systems that implement captive key can be awarded two credits or decrease the probability of an accident by a factor of 100. Captive key systems are a commonly thought of as a simple solution because they are retrofitted to the current system and require no adjustments for valves or equipment.
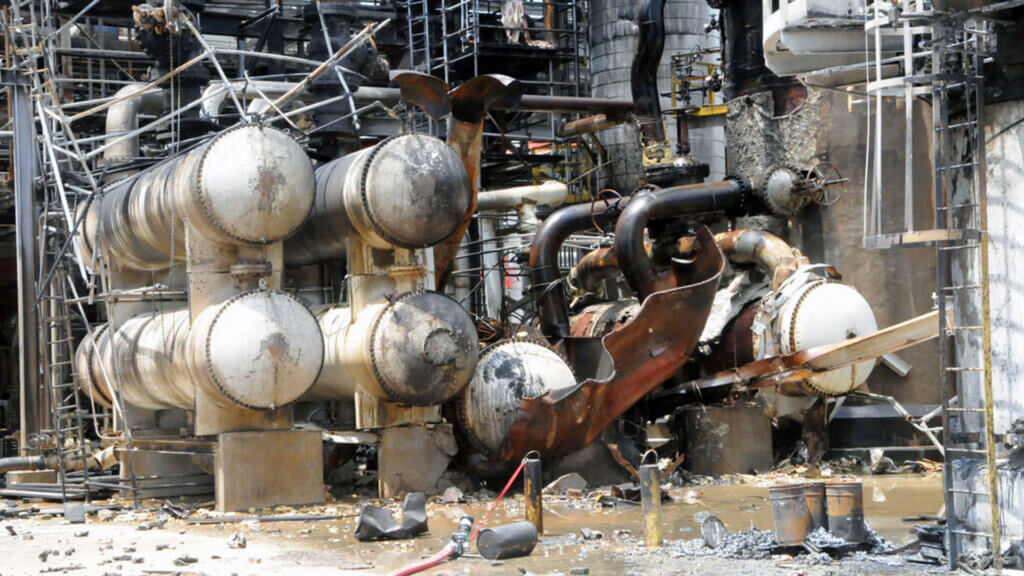
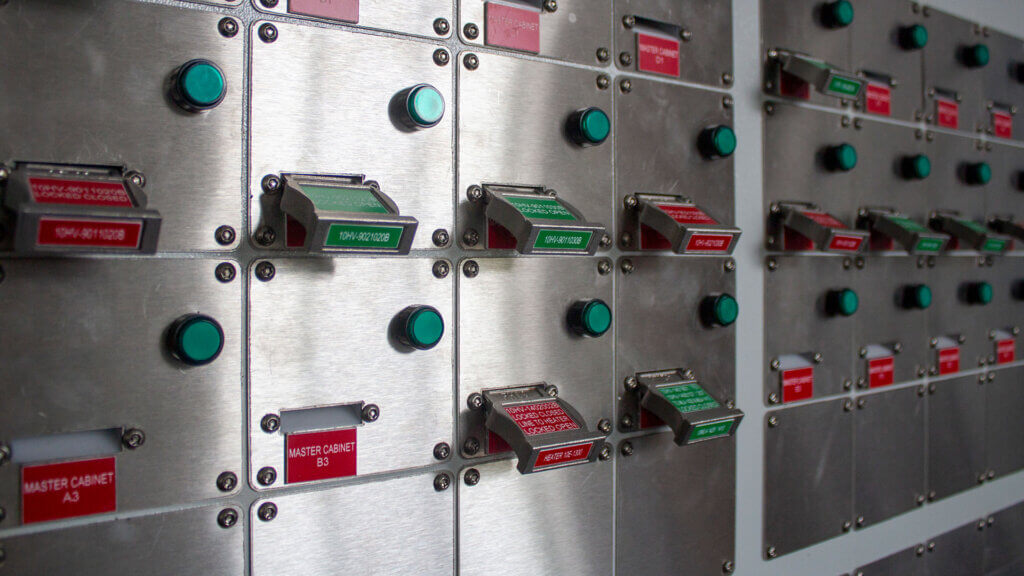
Download our whitepaper
Find out more on achieving risk reduction by implementing captive key systems!