How to avoid dangers when operating pig launchers and receivers?
Guaranteeing safe pipeline pigging operations
Pipeline pigging is a form of flow assurance, where pipeline pigs are used to purge, clean, and inspect pipelines to keep them running smoothly. It is a vital component of pipeline maintenance, operation, and integrity. Pigging helps improve pipeline flow, increase operating efficiency, and reduce costs and downtime. The main benefit of this type of maintenance is that it can be carried out without interrupting the process in operation. However, pigging operations are also high-risk events. Since the operation is hazardous, pigging is to be carried out by experienced professionals.
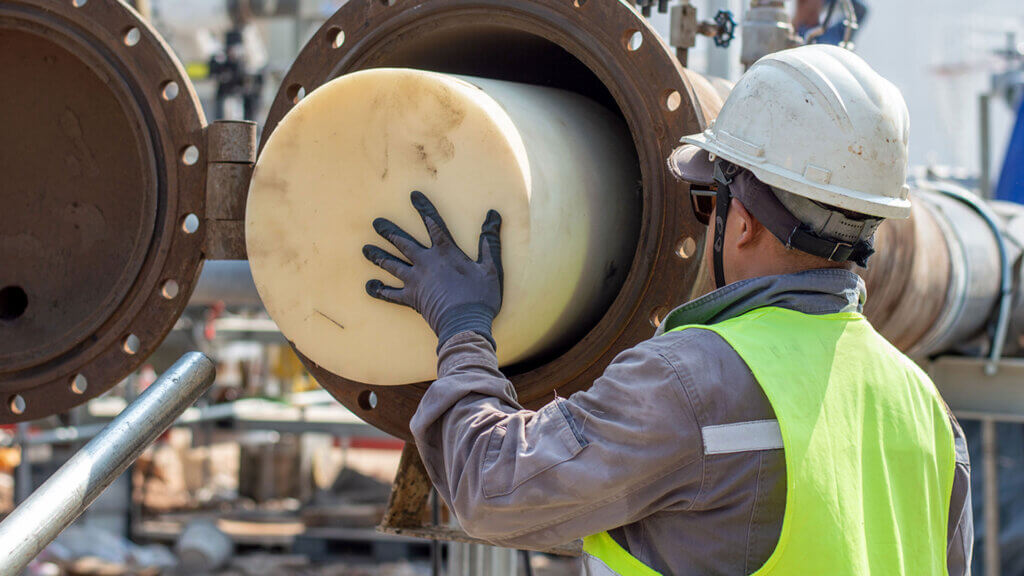
How pipeline pigging operations work
In its simplest form, a pigging system consists of a solid projectile or plug (the ‘pig’) with a diameter slightly larger than the pipeline or tubing that is transporting the liquid. Pipeline pigging works by introducing the pig into the pipeline and pushing it through the pipe. A launcher or receiver station is typically a vessel, connected in parallel to the existing pipeline. This allows launching or receiving the pig, using the pipeline’s normal operating pressure, and without interrupting the flow or production. The vessel is equipped with a closure door to load or offload a pig. Receiving or launching the pig involves several sequential valve operations, in combination with opening and closing the closure door. Pigging operations are dangerous, as opening a pig trap closure while there is pressure in the barrel can shoot the pig out of the launcher at high speeds. Attempting to pass a pig through a partially open outlet valve, or prematurely opening the pig trap in the presence of high levels of toxic hydrogen sulphide, can have fatal consequences.
Safety criteria
Before opening the closure safely, there are several basic safety criteria that need to be met.
- The vessel must be drained and depressurized.
- The vessel must be isolated from the process pipeline by closing the kicker lines and the main valves.
- In case of a closed drain systems and/or vent headers, the vessel must also be isolated by closing the drain and vent valves.
- The vessel needs to be free from toxic gasses like H2S.
- At the same time, the vessel must remain isolated when the door is open
- When the launching or receiving procedure starts, the closure should be properly closed.
- Since the pigging station is a bypass, there is also a potential danger that production is interrupted.
- when the throttle is not fully opened before starting to isolate the launcher and receiver station again.
Dangers of pigging operations
If safety criteria are not strictly met during pipeline pigging operations, incidents and accidents can occur due to incorrect valve operation procedures.
- The closure door is opened, while pressure still possibly remains inside the vessel.
- The main process valve is opened, while the closure door is still not yet fully or properly closed.
- The closure door is opened, while a high concentration level of H2S or other toxins remain inside the vessel.
- The vent valve remains open, while the vessel is being pressurized with its medium.
Procedures do not guarantee safe operations
Formal procedures can be set up to prevent opening the closure door under pressure. However, these are no guarantee that all safety criteria are taken into consideration. Many accidents have occurred all over the world during dangerous pigging maintenance operations, even with strict procedures in place. Operators can be trained to follow procedures and informed about potential dangers, but mistakes cannot be excluded.
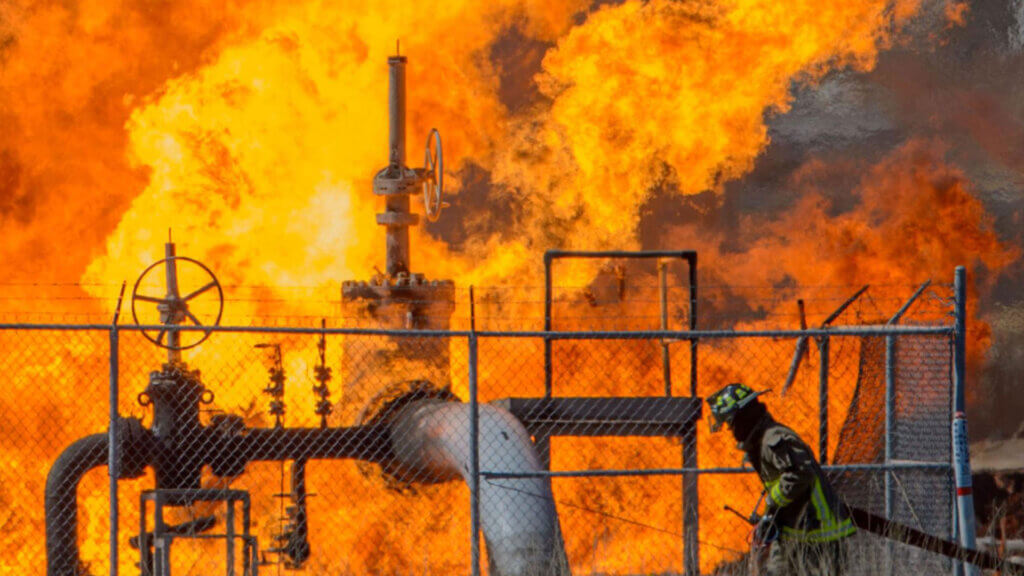
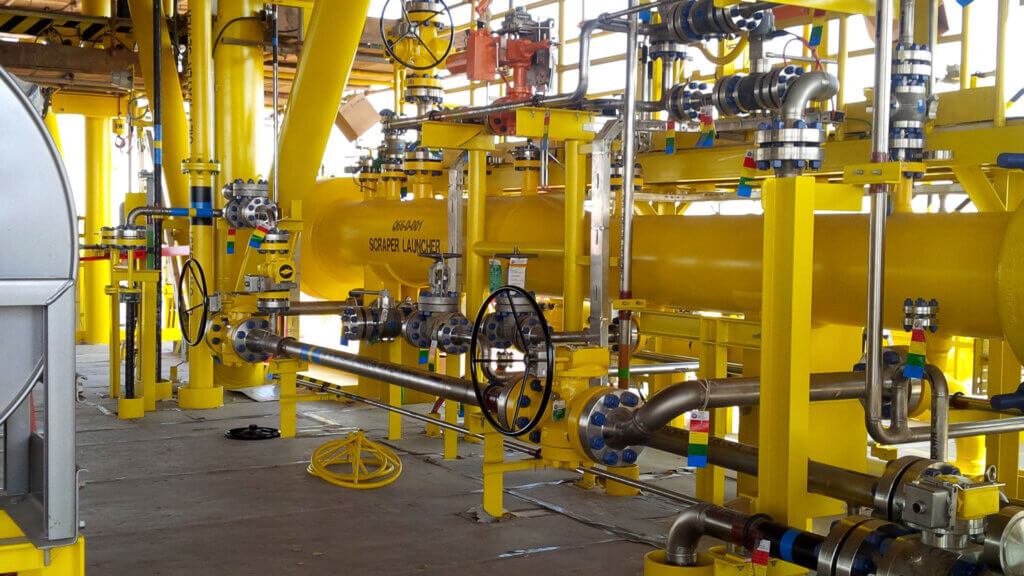
Pigging processes cannot be fully automated
Even though some larger valves are equipped with motor operated valves (MOV), the process cannot be fully automated, since the loading and offloading of the pig requires manual operations. Therefore, partially equipping MOV’s on valves does not sufficiently guarantee the safety of people and processes.
Written procedures and operating guidelines alone cannot ensure safe operations
To avoid dangers and incidents, such as loss of production time, or environmental damage, most companies have standard written operating procedures in place. In addition. most vessels are equipped with pressure and temperature transmitters to raise alarms. Written procedures and operating guidelines alone cannot ensure safe operations, as the human factor is not excluded. Alarms on the other hand do inform about sudden pressure and temperature increases, but this information is presented too late to act and prevent damage.
Guaranteeing safe pigging operation with valve interlocks
Valve interlock systems provide a simple, fail-safe process that ensures accidents cannot happen during a pigging operation.
- When starting a pigging operation, valve interlock keys are used to unlock and open the vent and drain valve respectively. These actions release a key that can then be used to open the vessel door safely and load the pig.
- Once the pig is loaded and the vessel door is closed and locked, a key is released to close the drain and vent. This action releases the key that opens the kicker valve and launches the pig.
- Once the pig is launched, the trap is re-isolated by closing and locking the mainline valve. This releases a sequence of keys that depressurise the trap by closing the kicker and opening the vent and drain.
- The last step involves closing all valves and returning the final key to the control room key cabinet, where is it kept until the process starts again.
Valve interlock systems must be operator friendly, and they should require no additional work effort from the operator other than normal procedures would require. They should also keep the process simple and transparent.
Prevent operating valves while closure door is fully open
Valve interlocking systems prevent operators to operate any process valve while the closure door is still open, or not in its fully locked closed position. This is because the key to start the operating sequence is still trapped in the closure door lock.
Guarantee venting and draining before opening the vessel
To ensure the safety of the operators while opening a closure door, the vessel involved needs to be vented, drained, purged, and isolated from the main process line. Vessel lay-outs vary, just as procedures, and from and HSE point of view it is therefore good practice to have valve interlocks mounted onto all critical valves. This way, these valves can only be operated according to procedure, and the vessel is clear of any pressure and toxic gasses.
Valve interlock operation sequences for pipeline pigging
Even the best procedures cannot fully prevent mistakes to happen, and for this reason they do not sufficiently guarantee the safety of people and processes. This would be especially true for pigging operations, where the effects of mistakes can be disastrous. Also routine tasks which involve working with dangerous pressure levels can have serious consequences when not carried out correctly. Modern valve interlocking solutions are the ultimate additional safety measure. They have proven to provide excellent safety levels for pigging operations. And they seamlessly integrate within operations, enabling operating companies to eliminate human error on pigging operations.
Our whitepaper on safe pigging operations contains more elaborate valve sequences, using additional sequence control products that address unusual conditions during a pigging procedure.
Guaranteeing correct purging and draining procedures with sequence control devices
H2S gasses are extremely dangerous. When H2S gases are trapped inside a vessel, it needs to be purged to remove these gases. The volume of the vessel and the H2S content determine how many times purging should take place. Often, vessels need to be purged at least 7 times before it’s safe to open the closure door. To guarantee that procedures are followed, an extra control unit is used in addition to standard valve interlocks. This unit guarantees correct purging procedures, without shortcuts. For example, when a vessel needs to be purged 7 times, the mechanical control unit is programmed to force operators to purge 7 times before opening the vessel. These steps cannot be skipped This will keep the integrity of the plant and the safety of the operator a priority.
Incorporate signals from other field devices
Additional sequence control products address unusual conditions during a pigging procedure. These products combine digital technology with traditional interlocking. Sequence control products bring signals from other field devices, like pressure or H2S/CO2 sensors, into the interlocking sequence, and only release keys for mechanical interlocking if all conditions in the process have been met. process variables – for example vessel pressure or H2S-levels – can be incorporated within safeguarded operating procedures. Electro-mechanics enable mechanical valve interlocks to be fully integrated within the context of a common system for control and safety of pigging operations. Additional safeguards, such as electrical signals from valve positioners via a switchbox, can also be incorporated in the system.
Combining mechanical and electronic safety measures
Recent developments in mechanical valve interlock products also made it possible to integrate valve interlocks within sophisticated electro-mechanical and PLC controlled cabinets, combining mechanical and electronic safety measures into one single safety system. These solutions allow for communicating detailed instructions, monitoring the status of the procedure and operating part of the sequence from the control room.