How to avoid dangers and guarantee safe LDPE processes?
Guaranteeing safe LDPE processes
Low-density polyethylene is the oldest type of polyethylene. It is produced in a high-pressure process. LDPE is a soft, tough, and flexible kind of polyethylene due to its highly branched molecular structure. When it is deformed, it can recover its original shape due to its natural elasticity. The ‘high pressure’ polyethylene shows a higher melt flow index (MFI) and therefore, processes easier than most other types of polyethylene.
The LDPE production process is complex and dangerous. It involves ultra-high pressure and medium temperature. During the LDPE production process, a small mistake can have disastrous consequences. Incorrect valve operations can lead to significant loss of containment, injuries, and considerable damage and disruption to the plant. For this reason, LDPE plants have adopted strict safety precautions and have extensive safety regulations in place.
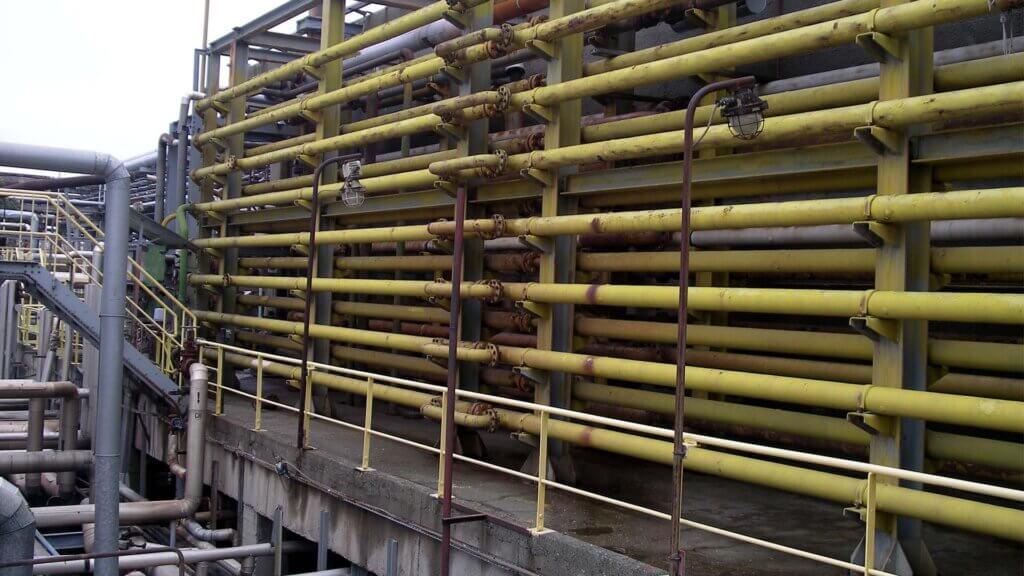
The LDPE production process in stages
The ethylene is cooled, compressed, and then placed into a reaction vessel where the polymerization process begins. In this process. about 20% of the ethylene gas is converted to polyethylene. The remaining ethylene can be recycled for further use. Additives like antioxidants and stabilizers are combined with the polyethylene. The molten polyethylene is then extruded into strings that can be cut into pellets that are cooled in water. The cool pellets are placed in a container where the water is removed and then added to a tower that will dry the newly formed material. After screening for any anomalies or fines by an air streaming process, the low-density polyethylene (LDPE) is removed and stored. Eventually, the LDPE will be packaged in bags and shipped out to manufacturers where the material will be re-melted and fashioned into finished products.
Environmental and safety issues
Even though LDPE High Pressure production technology can be well consolidated and mature, especially in the last decades, the market requirements in terms of quality and environmental impact of LDPE pushed plants to continuously update their technology, by improving equipment and by optimising the process cycle. An important role in plant design is played by environmental and safety issues.
Current risk mitigation measures are not adequate
As polymerization is highly sensitive to temperature and pressure fluctuation, emergency relief valves are required to prevent the runaway of a reaction. The pressure relief speed plays an important role in the safety integrity of reactor. Common practice is to monitor the relevant values as close as possible and react immediately in case of abnormal operation.
Safety procedures and administrative controls also play an important role in mitigating danger. Process hazard analysis tools like HAZOP are performed when new facilities are built, when new processes are introduced, or changes are made. They are also used review existing LDPE production operations and maintenance processes.
All these measures reduce the risk of human error, but do not completely remove it. Adopting engineering controls to remove risk should be the goal of every LDPE plant.
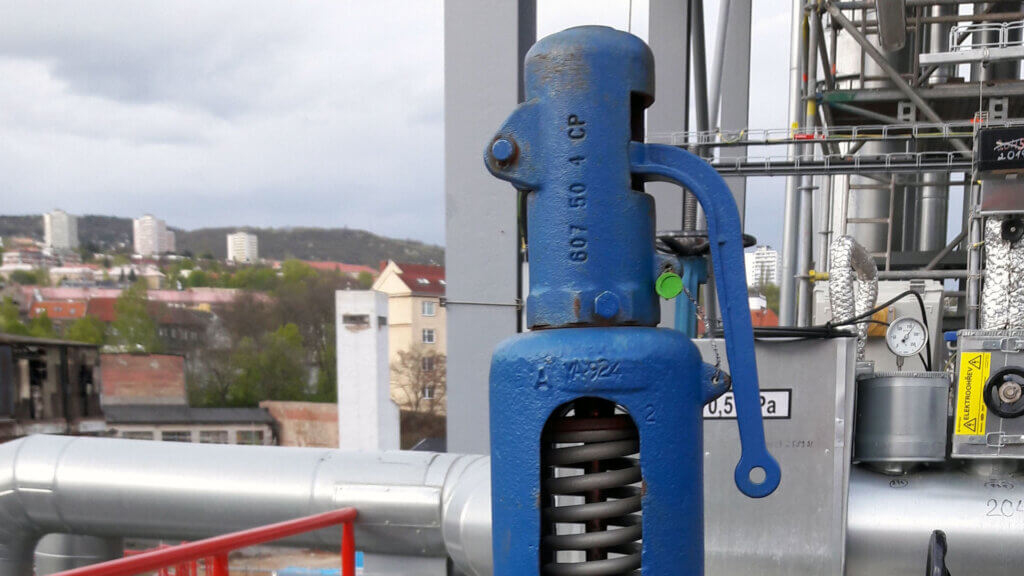
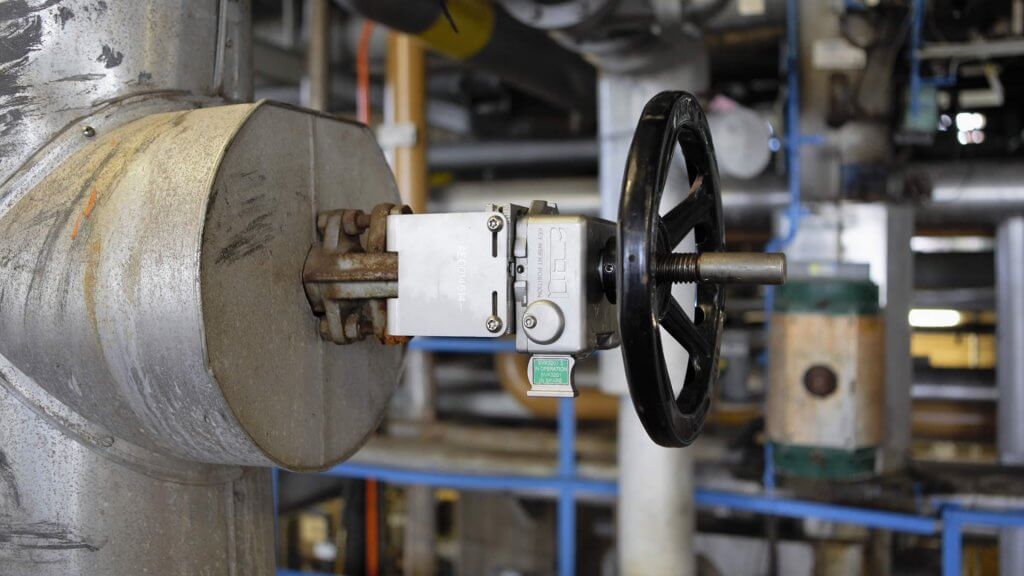
Guarantee correct valve line-ups with valve interlocks
To guarantee safe operations during LDPE production processes, valves always need to be operated in the correct order. This applies to ‘normal’ operations, as well as during maintenance and shutdown procedures. An effective and relatively simple solution for these complex operations employs the use of valve interlocks. Valve interlocks prevent the unauthorised movement of valves, and unique keys will only be released in the correct order, preventing operators from operating valves incorrectly. Valve interlock systems guide operators through manual valve sequences, confirm operating steps, prevent operators to operate valves when they are not allowed to, and provide visual indication of valve positions. An important feature includes the authorisation of access control to qualified or designated operators.
How to set up safe LDPE processes
Valve interlocks enable you to control critical LDPE process areas in a mechanical way. According to your plant’s process philosophy, all critical and relevant LDPE valve systems are equipped with valve interlocks. These critical line-ups usually involve an increase of pressure, or a blow-down. Especially for these kinds of operations, it is crucial that all valves are lined up correctly before operations can be started up. The keys of all interlocked systems are stored in a central key cabinet. Only if all keys are present in this cabinet, the process start up key can be removed, providing access to the ESD panel. If the ESD valve can not be operated, the process cannot be started-up.
How valve interlocks are used in LDPE operations
Mechanical valve interlock systems are widely used in many industries to ensure adherence to a safe sequence of operations. Specifically, during LDPE operations, they are used to safeguard many critical operations, such as:
- Correct line-up of all flare sub-headers and the main flare header to the flare, and closing of the reactor blow down vessel before the plant process can be started.
- Safe switch over of the flare sub header from normal operation mode to maintenance mode.
- Safe switch over of the flare gas collector and the main flare header from normal operation mode to maintenance mode.
- Guaranteeing that all isolation valves are fully closed before opening the vessel for manual inspection and cleaning.
- Ensuring that nitrogen bottles are lined up to the degassing silo, with the manual block valve locked open.
- Ensures safe refilling of nitrogen bottles that are used for nitrogen purge of a degassing silo
- Ensuring safe switch over of the vent line from normal operation mode to maintenance mode.
- Ensuring safe switch over of the steam supply for normal operation mode to special operation mode.
Securing blow down vessels
The removal of liquid contents of vessels and equipment during blowdown is critical to prevent its contribution to a fire or explosive incident. Special focus should be on the reactor blow down vessel, because of the additional equipment that is used, like radioactive sources and the bottom closure. During normal operation the bottom closure (manhole or door) of the reactor blow down vessel is closed. Safe opening and closing of the bottom closure can be effected by using valve interlocks. They guarantee that all isolation valves and radiation sources are fully closed, before opening the vessel for manual inspection and cleaning, and that the vessel is closed and all isolation valves and sources are opened again before restarting the plant.
Typically, the valves are handwheel operated manual valves, and usually the sources are manually operated. However, it is also possible to interlock pneumatically actuated radiation sources. This electromechanical solution allows to include electrical signals like position indications, pressure, temperature, or other electrical signals into a mechanical valve operation sequence.
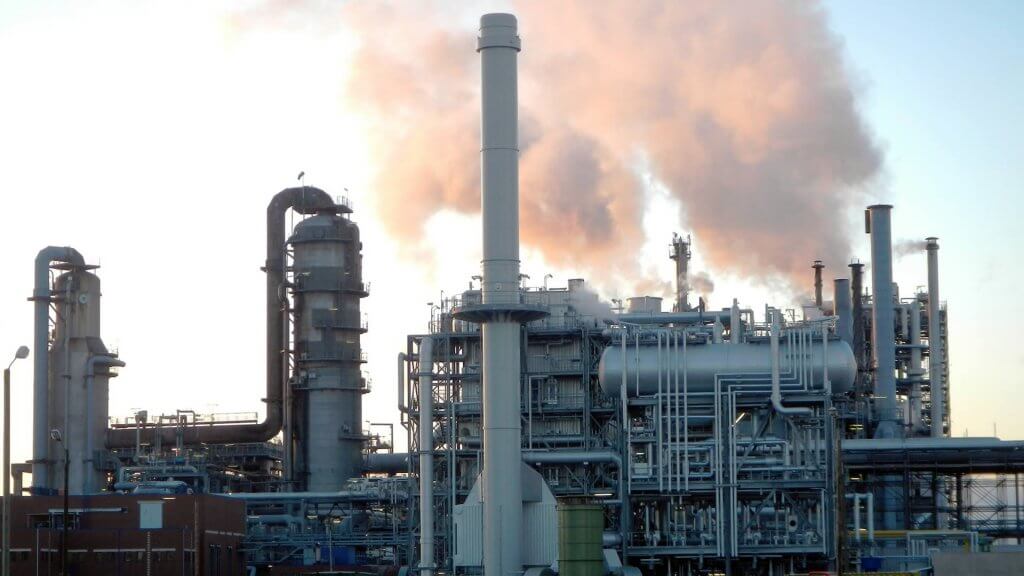
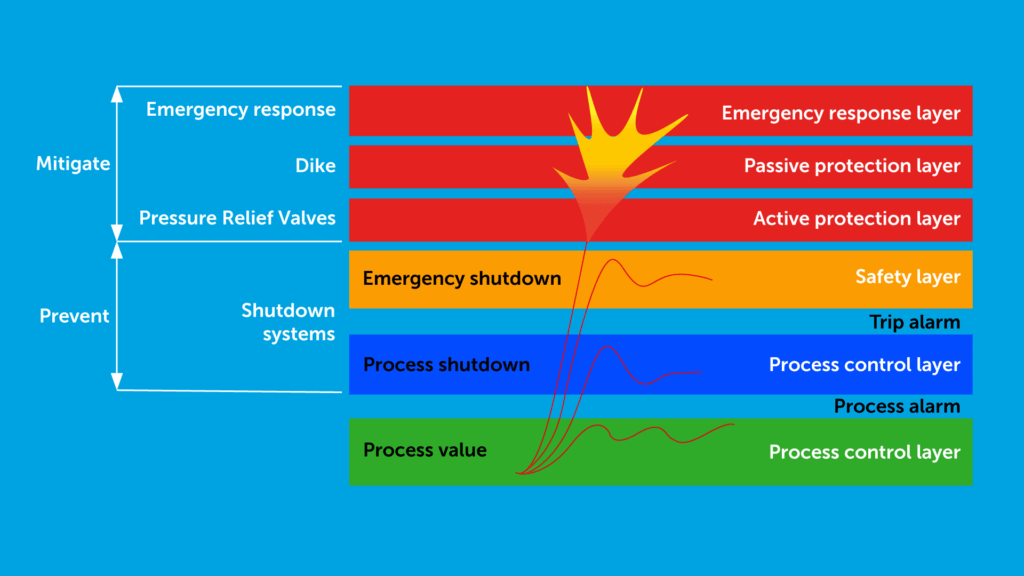
Create a physical barrier
In the industry, companies re-evaluate or review and the safety standards would the current or latest ones. In risks assessment exercises, such as HAZOPs, PHAs and LOPA, the risks per scenario can be reduced by either avoiding or mitigating the risk, to an acceptable level. As Sofis products create a physical barrier and provide administrative controls, the risk reduction can be awarded two points.