Using valve interlocks to eliminate risk in chemical offloading.
Ensuring safe valve line ups during chemical offloading in the water industry
How can you ensure operators offloading chemicals to the correct tank or line?
The offloading and transfer of hazardous chemicals is a common operation carried out at water treatment and wastewater treatment plants. The operation involves road tankers transferring highly hazardous chemicals into the plant for use in the drinking water or sewage treatment process. If done incorrectly, this process can potentially have dangerous health, safety, and environmental consequences.
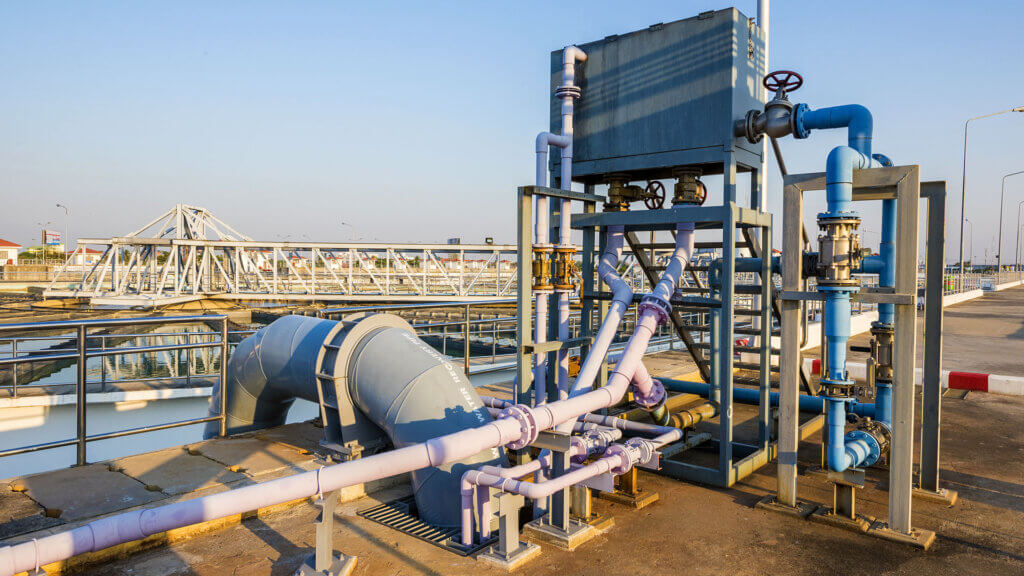
How are chemicals used in water and wastewater treatment?
At both water and wastewater treatment plants, chemicals are utilized to treat the water to a certain standard – for example, release into the environment and/or to be distributed as drinking water. There are many different types of chemicals that are used in the water treatment process, including coagulants, reducing agents, disinfectants, and heavy metal precipitants.
- Coagulants change the magnetic charge of particles such as arsenic, pathogens, and organic matter, in the water, causing them to attract and form larger clumps that can be more easily removed. Aluminium chloride is sometimes used as a coagulant, it’s highly corrosive and can cause severe skin burns and eye damage.
- Reducing agents bond to suspended compounds of harmful substances such as ozone, hydrogen peroxide, and biological compounds, to enable their settling and removal. Ozone, a commonly used reducing agent and disinfectant, is very reactive, corrosive and can be extremely irritating and potentially toxic to humans.
- Disinfectants, such as chlorine, chlorine dioxide, ozone, and hypochlorite, kill present microorganisms such as E. coli, giardia, and cryptosporidium, among others. All forms of chlorine are highly corrosive and toxic and exposure to high volumes of chlorine can lead to serious health problems.
- Heavy metal precipitants are added to facilitate the removal of heavy metals. Common chemicals used in heavy metal precipitation include sodium hypochlorite, sulphuric acid, and sodium hydroxide. All of which are corrosive individually, but when separately added in a certain order, enable heavy metal removal.
The chemical offloading process
At both water and wastewater treatment plants, the chemical offloading process is usually carried out in the following sequence:
- The tanker arrives at site and the tanker driver makes contact with a site representative to inform them of what chemical is being offloaded.
- The tanker arrives at the offloading bay. The offloading bay has a capture bund which ensures any accidental spillage from the process will be contained in the bund and safely drained away.
- Capture bunds typically have two routes for outfall – to a rainwater drain which goes into the watercourse, or to a chemical capture (blind) tank.
- Prior to commencing the chemical offloading process the driver or site operative must route the capture bund outfall to the chemical capture tank. To do this, the driver or site operative must close the valve to the rainwater drain and then open the valve to the chemical capture tank. This makes sure that if there are any spillages during offloading operations the harmful chemicals will NOT flow into the watercourse.
- Once the valves are in their correct position, the driver will connect the transfer hose to the tanker and plant offloading point, and then carry out the chemical offloading process.
- When offloading operations are complete, the driver will disconnect the transfer hose and reverse the capture bund flow routing. To reverse the capture bund flow routing the driver or plant operative will need to close the valve to the capture tank and then open the valve to the rainwater drain.
Not only is it critical for the driver to ensure that the capture bund flow is routing to the capture tank, but it is also critical to ensure that the chemical being offloaded is transferred to the correct fill line. Often there are numerous different tanks, manholes and connections at a water or wastewater treatment plant, therefore prior to connecting the transfer hose, the driver must be certain that the hose is connected to the correct transfer point on the plant, otherwise it could lead to a potentially catastrophic adverse chemical reaction, or accidental routing into a drinking water main.
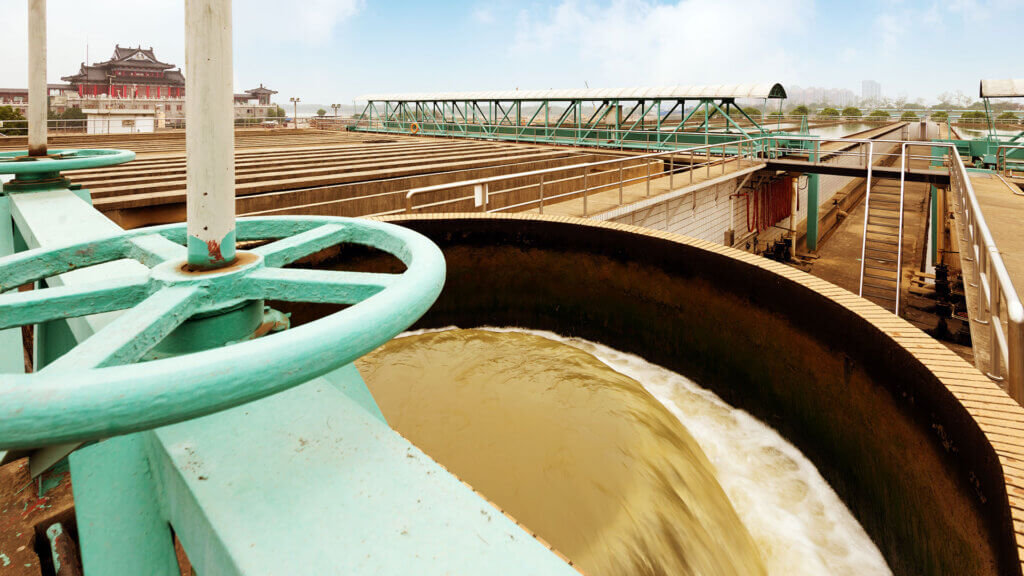
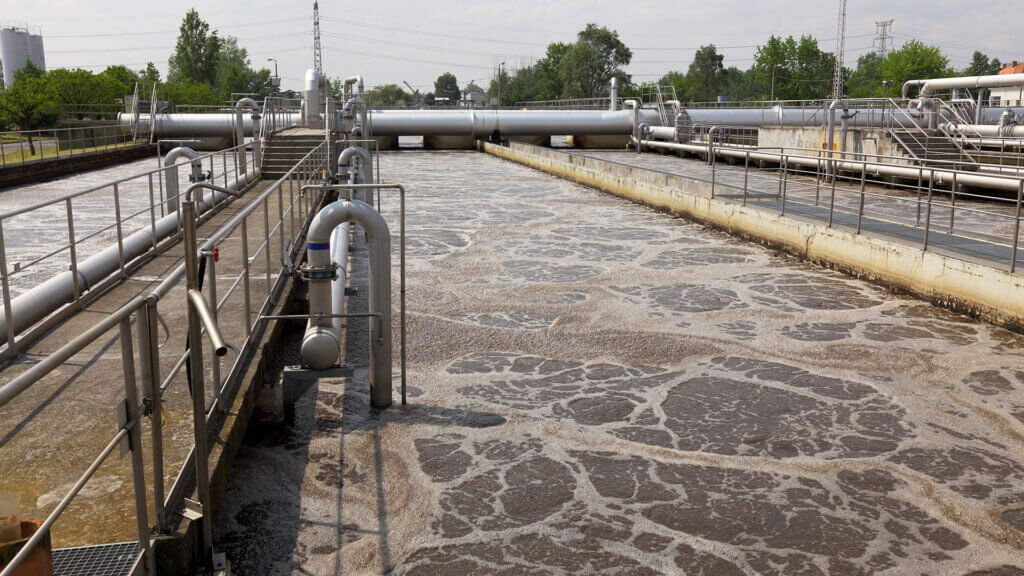
Hazards of chemical offloading
Contamination of drinking water caused by incorrect connection to fill point
Chemical offloading is a critical process in water treatment, if not controlled and executed properly it can have immeasurable health and environmental consequences. The Camelford disaster may be Britain’s worst water poisoning event, which occurred as a result of human error during chemical offloading.
A late and rushed driver arrived at a water treatment plant near Camelford in 1988 to deliver 20 tons of aluminium sulphate, which is commonly used in water treatment as a coagulant. When he arrived at the plant, he found multiple tanks and manhole covers in the offloading area. With little instruction from the plant and confused on which tank to empty into, he accidentally transferred the aluminium sulphate to a line that flowed into the drinking water for around 20,000 people in the area. Residents immediately began experiencing ill effects due to the contamination and grew concerned that they had experienced a harmful accumulation of aluminium in their bodies due to this incident. Their concern was only heightened after a resident of Camelford died from a rare neurological disease and upon examination, her brain was found to have a high concentration of aluminium.
While the true effects of the Camelford disaster may never be known, what is known is that it was fatal for at least one person and caused ill health for many others. A safety mechanical interlocking system could have prevented the driver from offloading into the incorrect fill point, which could have prevented the contamination of the drinking water and could have prevented the fatal consequences of the contamination.
Dangerous chemical reactions caused by incorrect connection to fill point
Numerous chemical spills, sometimes resulting in explosions, evacuations of surrounding areas, and hospitalizations for affected workers, have been reported at water and wastewater treatment facilities around the world. A portion of these incidents have resulted from errors during the chemical offloading process.
For example, the town of Martinsburg, West Virginia in the United States had to be partially evacuated in 2019 when a spill occurred during chemical offloading at a wastewater treatment plant. The incident occurred when sodium hypochlorite and ferric chloride, two common heavy metal precipitants used in wastewater treatment, were accidentally mixed during a transport tanker offload.
In 2022, another incident occurred at a wastewater treatment plant in Bedford, Virginia in the United States when two chemicals were mixed during offloading, which created a large amount of chlorine gas. Four people were treated for non-life-threatening injuries because of exposure to the chlorine gas.
The installation of a safety interlock system on the transfer location could have mitigated these incidents by guaranteeing that the fill hose could only connected to the correct fill point, and thus eliminating human error in the selection of fill points in the chemical offloading process.
Current offloading solutions
In chemical offloading, the safety of the process depends entirely on the human element of the driver or site operative manually checking and verifying that the rainwater drain and capture tank valves are in the correct position, and also ensuring that they are offloading to the correct fill point. If these checks are not carried out correctly and/or the operative makes a mistake, there is an increased risk of chemicals entering the rainwater watercourse, entering the wrong tank, or even entering the drinking water main.
Current control measures for reducing the risks in chemical offloading control include written and colour-coordinated instructions, and a standard procedure of double-checking valve positions before offloading. Both aforementioned control measures still contain the risk of human error, therefore further control barriers should be considered to reduce and/or eliminate the human error potential.
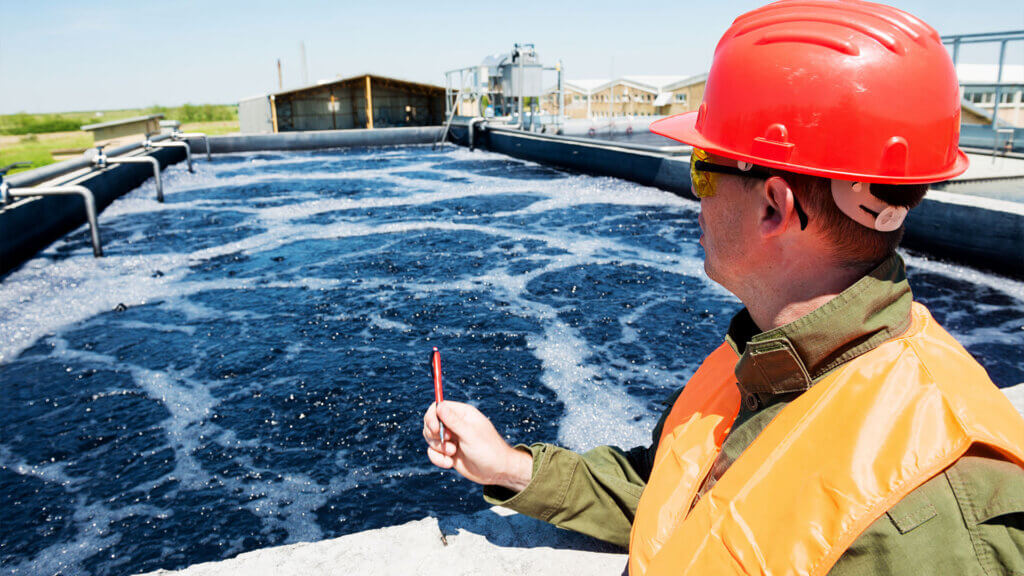
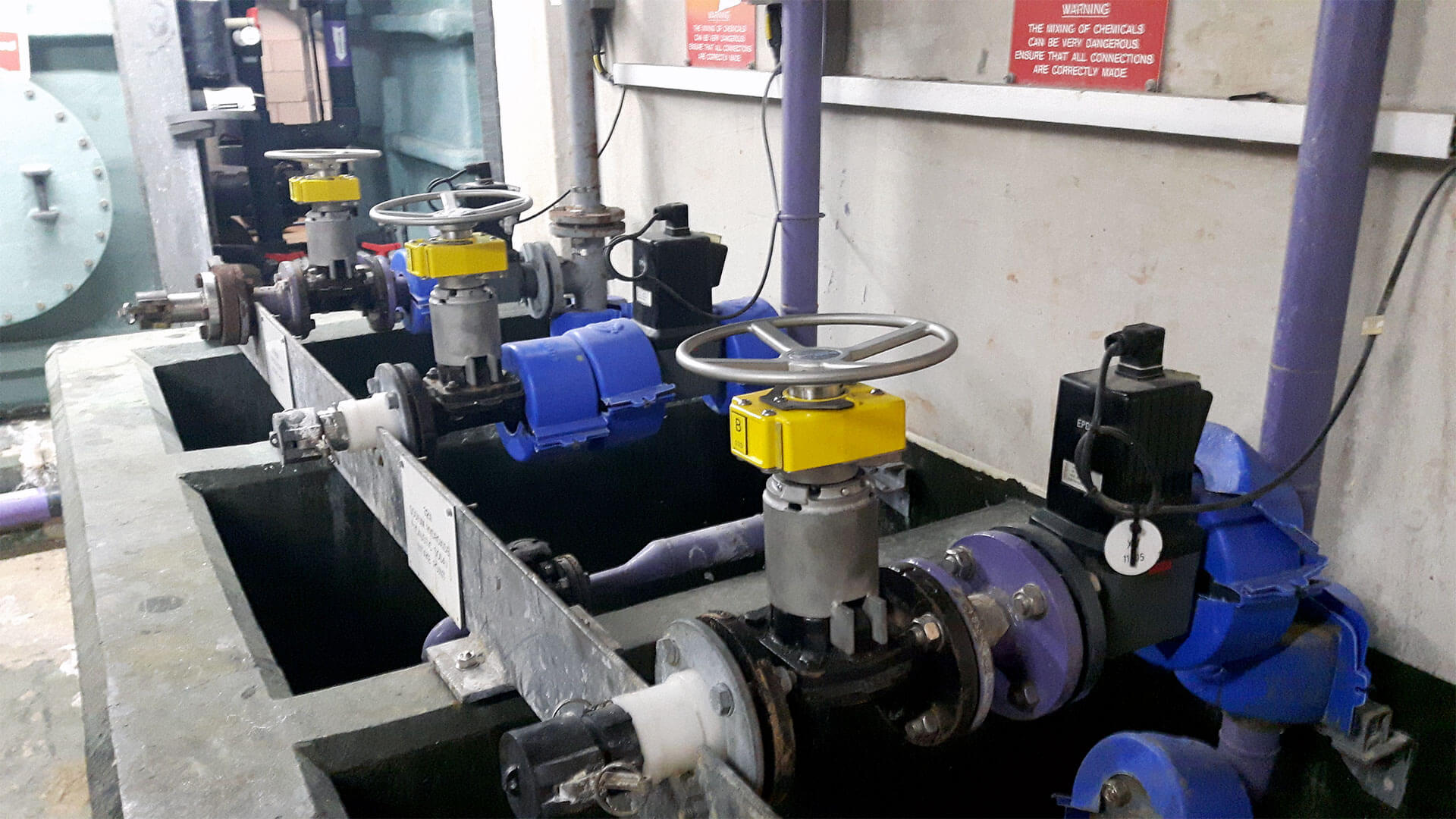
Using mechanical interlocks to reduce risk in chemical offloading
Mechanical interlocks can provide engineered control measures to control the processes of the opening and closing of system valves, and the connection of hoses to plant fill points.
At a water or wastewater treatment plant, mechanical interlocks can be utilized to enforce a predetermined valve operation sequence. This sequence ensures that the rainwater drain valve is closed and the chemical capture tank valve is opened before the driver can access the chemical offloading point.
Trapped key system
Mechanical interlocks can also be deployed at every tank, manhole and connection point to ensure offloading and transferring of chemicals takes place into the intended line. Mechanical interlocking systems require the operator to obtain the correct system key from a controlled location; this could be a control room, control centre, or via an electronic key distribution control cabinet. The interlock system keys are uniquely coded to ensure that the key can only operate the intended interlock. The trapped key system ensures the operator can only ever operate the relevant valves and connection points in a predetermined sequence.
Sofis valve interlocks significantly reduce the risk of an incident in offloading operations which could result in a chemical entering the watercourse, entering an unintended tank, or even entering the drinking water main. To reduce risk and ensure compliance in your chemical offloading operations contact one of our team now.
Do you want to know how to guarantee safe chemical offloading operations?
We have extensive application knowledge and over 30 years of experience and project management skills. Our global team of engineers is available to assist with interlock sequence design and develop customized process safety solutions.
Guaranteeing compliant offloading
On- and offloading needs to be correct every single time. Errors can cause loss of product, down time and they can damage your reputation. However, often it involves manual operations. Incidents happen. Sofis can ensure your operation is compliant – avoiding spills, contamination and loading or offloading of the wrong product. Preventing errors before they can occur, increasing efficiency, sustainability and protecting your brand name.